NTV — Testing and Prototyping Department
Important (secret) laboratory work
Laboratory work at nass magnet may — as the title suggests — seem secretive to some employees. This raises the question: „What exactly does the laboratory at nass magnet do?“ We would like to take this opportunity to introduce the laboratory in a little more detail.
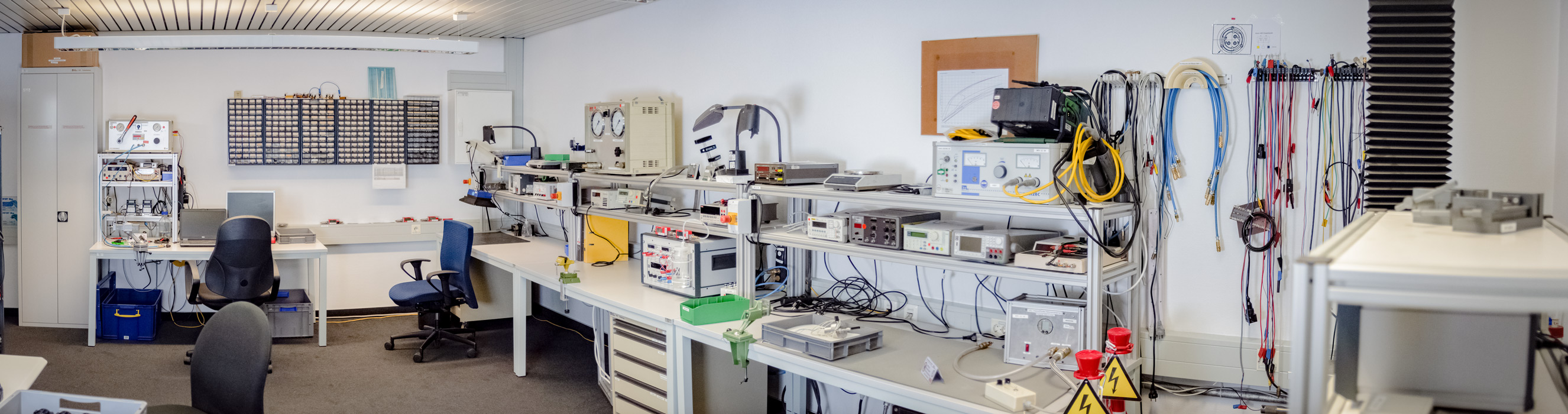
The lab, as it is called on the grapevine, actually bears the name NTV – Testing and Prototyping. The „N“ stands for „nass magnet“, the „T“ for „technology“ and the „V“ for „testing“ (from the German word „Versuch“). Due to this department abbreviation, it is often confused with Sales (NKV) or Logistics (NTL).
The team currently consists of six test engineers, two experiment specialists, a tester, a test mechanic and two working students. Testing and prototyping, which accommodates two further prototyping specialists, is currently still part of the NTV department. This is located on the upper hall level.
Three of the in-house laboratories are located (or rather, hidden) in the company basement, which means that the work carried out there is not visible to everyone. In addition, the fourth floor houses the „electronics laboratory“, as well as its associated offices. The multitude of laboratories stems from the different testing options and activities. In the future, we plan to house all laboratories in the basement in order to keep the distance between labs short and use our office capacities optimally.
Testing tasks consist of planning, performing and documenting tests. In terms of output, in the first instance testing produces test plans, results and reports. Everything related to the function of our products — mainly solenoid valves — falls into this area. Thus, testing is an important component of development at nass magnet.
The work spectrum ranges from simple function tests to tests under different environmental conditions, to service life tests and misuse tests. Because Testing is responsible for all products developed at nass magnet, our work is very varied. The majority of our work is made up of development products, that is, work with prototypes, and for this our day-to-day work is performed in both the lab and the office.
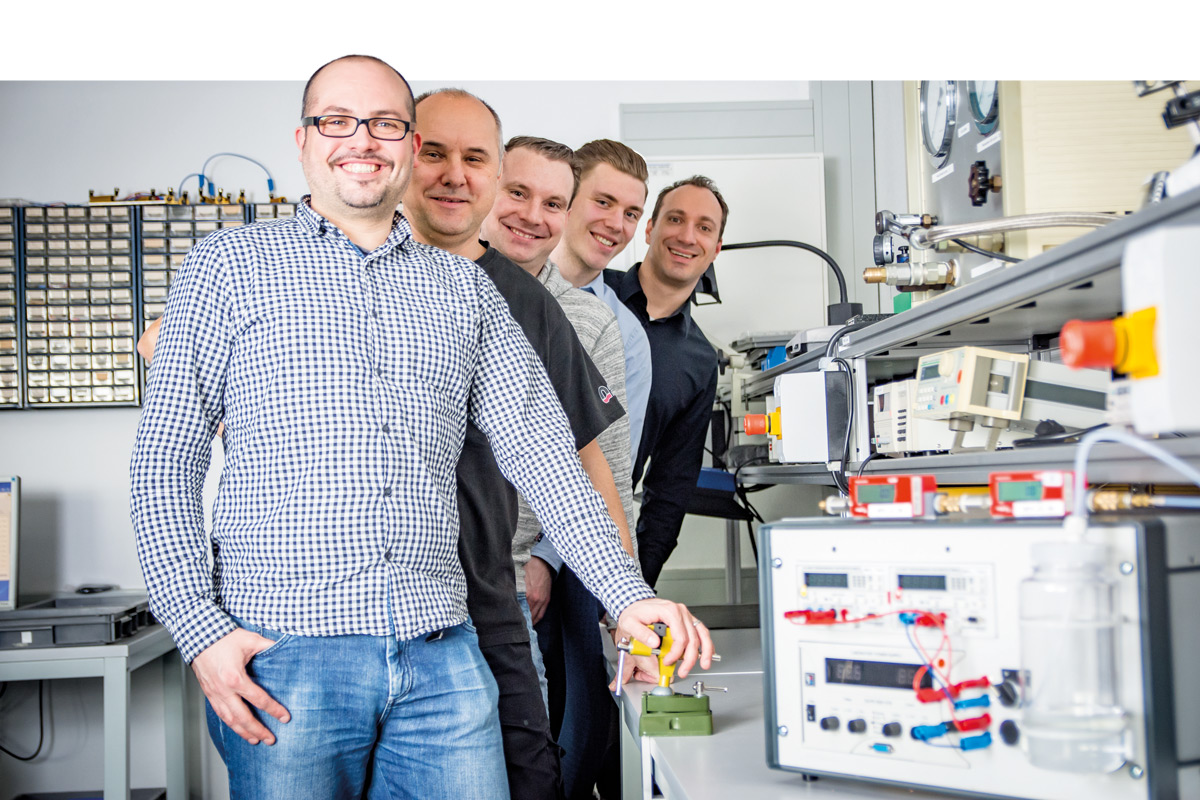
In this day and age, we are increasingly faced with the question of why we even need tests any more – after all, with modern technology one can calculate and simulate almost anything. With the NTE, NTK and PTK departments, our organisation is home to high-performance development teams. The assumption that the number of tests needed for product development and series production is decreasing, is false. In fact, the number of necessary (experimental) tests has actually increased in recent years. This is in part because nass magnet has supported new developments on an experimental basis, and also because our customers are always demanding more complex verification tests.
The tests are highly relevant, all reports have to be saved and test specimens (test parts) stored. Above all, due to the automotive projects that have continued to increase in number in recent years, the testing requirements have escalated rapidly. By way of illustration, here are a few figures, data and facts that support our daily work in the laboratory:
Meanwhile, it is part of our standard to test our (automotive) products thoroughly in temperature ranges from -40 °C to 130 °C, at pressures of up to 25 bar.
One of our newest environmental simulation chambers, for example, allows us to produce a temperature shock in a 2-chamber procedure, i.e. transferring the test specimens from, for instance, 130 °C to -40 °C – a temperature difference of 170 K – within less than 10 seconds. This highly extreme material test is a good example of how we are constantly adapting to the requirements made of us, and continuing to develop. We can also simulate a tropical climate, for example, with air humidity above 90% relative humidity. Common misuse tests include impact and drop tests, or coil heating measurements with temperatures above 180 °C, which may lead to the coil melting. Burst pressure tests, which cause solenoid valves to burst at pressures up to 160 bar, are also worth mentioning.
The statement „In testing, solenoid valves are tested until they break“ is, therefore, absolutely right.
To develop and release a new solenoid valve, multiple tests are required. These test series, designated as validation, are planned exactly in accordance with customer specifications (specification sheet) as well as valid standards, coordinated with the customer, executed, documented and evaluated. It can easily take six months or longer to perform a product validation. Many individual tests lead to the overall result for the product tested.
To develop and release a new solenoid valve, multiple tests are required. These test series, designated as validation, are planned exactly in accordance with customer specifications (specification sheet) as well as valid standards, coordinated with the customer, executed, documented and evaluated. It can easily take six months or longer to perform a product validation. Many individual tests lead to the overall result for the product tested.
The most important thing is that results and findings of the tests flow directly into product development and improvement. Every product fault and abnormality that is found in the prototype during testing is valuable for nass magnet. This is because they represent an opportunity to improve and rectify the faults before they occur with the customer, or later in the field (possible recall action). Therefore, laboratory work makes a very important contribution to the functionality and safety of nass magnet products.
The requirements made of Testing lead to lasting further development of the laboratories, as well as the competence of the entire team. Nevertheless, we cannot perform all tests ourselves. For rare or highly specialised tests, we work together with accredited external laboratories.
Our laboratory work is characterised above all by highly conscientious working methods and documentation, as well as experience with all of our own products. If a test delivers „poor“ measurement results, this is also documented as such. Truthful reporting and corresponding communication with development engineers and customers form the basis for our testing work. Experience shows that this is not always met with enthusiasm at first, as the value of our work is sometimes not recognised until later on.
Above all, the IATF16949 audit increases the quality requirements imposed on the tests. As a result of this, the optimisations made in testing at present are primarily organisational ones. A major challenge in the future will be the planning and execution of so-called requalifications, which are selected retests of products in series that have already been tested. This is intended to ensure long-term product safety.
Fifteen years ago, the nass magnet laboratory was still staffed by four employees. Since then, the current number of employees has grown to indicate not only development but also challenges. In addition to the testing employees at our Hanover location, a laboratory has also been built in the last few months at the N-HU site, for which our Hungarian colleague Szilard Pál is responsible. This one-man lab will be receiving reinforcements in the near future.
Currently, testing is focussing on cable/plug connectors, as well as on the execution of IP tests (dust and waterproofing tests). Expansion of the testing possibilities and methodical expertise is in progress. The laboratory at the N-HU site, which works in line with the same quality standard as the lab at the N-DE site, will be presented in more detail in an upcoming issue of iMAGE.
From an organisational perspective, Testing and Prototyping is part of the NTV department. Its main tasks are to create samples and prototypes. This work has become increasingly relevant to customers, particularly in recent months.
Meanwhile, small-scale series of prototypes in quantities of up to 5000 pieces are planned, produced, tested, optimised and documented in Testing and Prototyping. This change has led to a strategic modification being developed jointly and approved by management: Testing and Prototyping is to be transformed into a process laboratory over the coming months.
NTV — measuring brings knowledge!
Sebastian Otto
Head of Testing and Prototyping
nass magnet GmbH