3D-Druck bei nass magnet
Schicht für Schicht zur Innovation
Die Anwendungsbereiche für den 3D-Druck sind mittlerweile beinahe grenzenlos. Vom Prototypen und Anschauungsmodell mit einer Stückzahl von 1, über Ersatzteile bis hin zu Kleinserien — die denk- und kostengünstig umsetzbaren Möglichkeiten sind weit gefächert.
Umsetzbare Möglichkeiten
Konzeptmodelle (Prototypen)
Schnelle und einfache Herstellung von Modellen zur Vorstellung und Prüfung erster Konzepte eines neuen Produktes
Funktionsmuster
Je nach verwendetem Verfahren, Material und Modell erreichen diese Bauteile eine Stabilität, die es ermöglicht, Modelle auf ihre Funktionen zu testen
Kleinserien
Moderne Industriedrucker ermöglichen, durch hohe Druckgeschwindigkeit und Zuverlässigkeit, Kleinserien bis Jahresstückzahlen <1000
Spritzgussformen
Auch Einsätze für Spritzgusswerkzeuge lassen sich für erste Schüsse mit dem 3D-Druck herstellen und anschließend prüfen, bevor verbindliche Entscheidungen über teure Werkzeuge getroffen werden
Montagewerkzeuge/Montagehilfen
Der Einsatz von 3D-gedruckten Montagewerkzeugen und Montagehilfen in der Produktion spart Zeit und Kosten, zudem wird die Ergonomie für Mitarbeitende erhöht.
Ersatzteile
können schnell und einfach selbst gedruckt werden, auch wenn z.B. keine Ersatzteile mehr verfügbar sind oder bei Lieferanten die Lieferzeit zu lang wäre. Aber auch Lieferanten müssen nicht mehr über mehrere Jahre nach Produktionsende Ersatzteile bereithalten, sondern können diese auf Nachfrage des Kunden drucken.
Marketing Modelle/Mock-up
Herstellung von Modellen oder Werbemitteln für potentielle Kunden auf z.B. Messen
Gewinnbringende Vorteile
Designfreiheit
Höhere Designfreiheit durch Entfall von fertigungsbedingten Restriktionen in der Konstruktion
Zeitersparnis
Kurzer Produktentwicklungszyklus, schnellere Entdeckung von Fehlern in der Konstruktion, kurze Anpassungszeit, schnelle Umsetzung
Kostenreduzierung
Fehler im Entwicklungsprozess vom Entwurf bis zur Fertigung steigen exponentiell an. Durch Fehlervermeidung und kürzere Durchlaufzeiten können die Kosten deutlich reduziert werden.
Geheimhaltung
Entscheidend bei der Entwicklung neuer Produkte ist die Geheimhaltung von Projektdaten
Einfacher Druckprozess
Der Ausgabeprozess auf einem 3D-Drucker ist fast so einfach wie die Erstellung eines Farbdruckes auf Papier.
Bürotaugliche Anwendung
Die 3D-Drucker können direkt im Büro aufgestellt werden. Denn sie sind voll bürotauglich, leise und ohne störende Emissionen.
Allgemein wird beim 3D-Druck das Objekt additiv gefertigt. Das bedeutet, es wird Material hinzugefügt und so Schicht für Schicht aufgebaut. Dieses Verfahren schont nicht nur unsere Ressourcen, sondern es lassen sich auch komplexe Geometrien realisieren, die mit herkömmlichen - subtraktiven Verfahren - gar nicht oder nur mit sehr hohem Kosten- und Zeitaufwand möglich sind.
Prozesstechnisch bietet die additive Fertigung den großen Vorteil, Ideen direkt zu realisieren, Bauteile bzw. Vorrichtungen zu testen und flexibel bis zur Serienreife anzupassen — alles vollkommen unabhängig von Lieferanten. Dadurch können Durchlaufzeiten verkürzt und so auch die Entwicklungs- und Fertigungskosten sehr geringgehalten werden.
Übersicht der wichtigsten 3D-Druckverfahren
Die aktuell wichtigsten 3D-Druckverfahren lassen sich in die drei Kategorien aufteilen: Freiraumverfahren, Flüssigverfahren und Pulververfahren. Hauptsächlich finden hierbei die beiden Materialgruppen Polymere und Metalle Verwendung. Ausgangspunkt für ein 3D-Druck-Objekt ist immer ein digitales Modell.
Freiraum-Verfahren
Den meisten dürfte das FDM Verfahren bereits bekannt sein, da dieses durch stark gesunkene Preise und einfaches Handling im Privat- und Hobbybereich bereits Einzug gehalten hat.
Einfach erklärt wird hierbei ein auf einer Rolle aufgewickelter schmelzfähiger Kunststofffaden, das sogenannte Filament, mit Hilfe einer Fördereinrichtung in den Druckkopf geschoben. In diesem Druckkopf wird das Material im Hot-End über die Schmelztemperatur erhitzt und durch eine feine Düse gedrückt und so ein noch dünnerer Faden erzeugt - ähnlich wie bei einer Heißklebepistole.
So kann Schicht für Schicht gefüllt werden und ein dreidimensionales Modell entsteht auf dem Druckbett. Der Druckkopf hängt dabei meist an einem Portalgestell und kann sich über Elektromotoren entlang der X- und Y-Achse bewegen. Dadurch werden die Fäden innerhalb einer Schicht zu einer Fläche verbunden. Ist diese Schicht abgeschlossen, wird der Druckkopf um eine Schichtdicke (Layer) entlang der Z-Achse angehoben und so die nächste Schicht auf die vorherige, abgekühlte Schicht gelegt, bis das vollständige 3D-Modell hergestellt ist.
Das zuvor in einem CAD-Programm erstellt Modell muss also vorher mit Hilfe einer Software in horizontale Schichten geteilt und in eine entsprechende Anweisung für die Ansteuerung der Motoren übersetzt werden. Die Anweisungen für die Ansteuerung der Motoren lässt sich mit Hilfe einer sogenannten Slicer-Software erstellen und an den Drucker übertragen. Um bestmögliche Druckergebnisse zu erzielen, lassen sich in der Software viele weitere Druckparameter einstellen. Nach Fertigstellung des Drucks müssen dem Teil ggf. noch Stützstrukturen entfernt werden, weitere Nachbehandlungen sind jedoch nicht erforderlich.
Flüssiges Material
Beim Rapid Prototyping (schneller Modellbau) Verfahren Stereolithografie, kurz SLA, entsteht das Werkstück aus einem Flüssigbad aus Photopolymer (Kunstharz). Ein dünner Laserstrahl fährt bei jedem Schritt Bahn für Bahn über den Ausgangsstoff und härtet ihn dabei aus, um die gewünschte Form zu schaffen. Schicht für Schicht hebt sich das Druckbett dabei von dem Flüssigbad weg. Das Teil wird dabei sozusagen kopfüber aus dem Photopolymer gezogen. Dabei müssen meistens kleine Stützpunkte erstellt werden, die später manuell entfernt werden müssen. Da sich der punktuelle Laserstrahl sehr schnell beim Druck durch das flüssige Material bewegt, wird das Material nur so weit ausgehärtet, dass es formstabil ist. Meistens müssen die Modelle dann zur vollständigen Aushärtung noch in eine UV-Kabine.
Polygraphie/Polyjet-/Inkjet-Verfahren
Polygrafie - auch bekannt als Polyjet- oder Inkjet-Verfahren - ist ein 3D Druckverfahren, bei dem Schicht für Schicht ein Photopolymer aufgebracht und anschließend mittels UV-Licht ausgehärtet wird. Im Detail: Das Bauteil wird durch einen Druckkopf, der ähnlich wie der Druckkopf eines Tintenstrahldruckers arbeitet, schichtweise aufgebaut. Damit es möglich ist, Überhänge an den Objekten zu drucken, wird Stützmaterial mitgedruckt. Deshalb verfügen 3D-Drucker über zwei oder auch mehrere Druckköpfe: Abwechselnd wird Bau- und Stützmaterial verdruckt. Schicht für Schicht werden die Konturen des Objekts auf der Bauplattform aufgespritzt. Als Material wird ein haltbares und formbeständiges Photopolymer verwendet. Das zunächst im Drucker flüssige Material verhärtet sich, wenn Schicht für Schicht nacheinander mit UV-Licht belichtet wird.
Pulverförmiges Material
Unter „Sintern“ wird ein Rapid Prototyping Verfahren verstanden, bei dem die Herstellung von 3D-Modellen mithilfe eines Laserstrahls erfolgt. Das Ausgangsmaterial liegt in feiner Pulverschicht, deren Partikel der Laser verschmilzt und so das Pulver Schicht für Schicht miteinander verbindet. Demnach werden über das Selektive Lasersintern (SLS) räumliche Strukturen aus einem pulverförmigen Ausgangsstoff hergestellt. Dabei ist die Verarbeitung von verschiedenen kunststoffähnlichen Materialien möglich. SLS verschmilzt selektiv Pulvermaterialien wie Nylon, Elastomere, Alumide oder Polyamide.
Selektives Laserschmelzen (SLM)
Allzu sehr unterscheidet sich das SLM-Verfahren nicht vom SLS-Verfahren. Anders als beim Selektiven Lasersintern (SLS) wird jedoch beim Selektiven Laserschmelzen (SLM) das Materialpulver nicht gesintert. Beim SLM-Verfahren wird das Materialpulver direkt an dem Bearbeitungspunkt durch die Wärmeenergie eines Laserstrahls lokal aufgeschmolzen. Der Bauraum mit dem Pulvermaterial wird bis knapp unter die Schmelztemperatur erhitzt. Damit das Material nicht oxidiert, wird meistens der Arbeitsraum mit einem Schutzgas gefüllt.
Die Suche nach dem richtigen 3D-Drucker für nass magnet
Die Erarbeitung erfolgte in Zusammenarbeit mit den Abteilungen NTE, NKV-P und NEP. Dafür wurden zunächst die folgenden möglichen Anwendungsgebiete für die weitere Auslegung betrachtet
- Prototypen-/Musterbau
- Prototypenwerkzeuge, Serienwerkzeuge und einzelne Komponenten im Vorrichtungsbau (Halterungen, WT-Führungen, Testaufbauten)
- Verpackungen für Prototypen und Muster
Hierbei trafen wir allerdings auch schnell auf einige Fragen über die Materialeigenschaften, Kosten, Verfahren und auch bei den ersten Anfragen bei 3D-Drucker-Herstellern, benötigten diese einige weitere Informationen von uns:
- Welche Materialien können/sollen verarbeitet werden?
- Welche Dauergebrauchstemperaturen haben die Materialien?
- Welche Festigkeiten werden benötigt?
- Oberflächengüte/Aussehen?
- Wie verhalten sich die Materialeigenschafen über die Zeit?
- Welche Toleranzen können eingehalten werden?
- Welche Stückzahlen?
- Anschaffungskosten/Budget?
- Folgekosten?
- Aufwand für gesamten Druckprozess?
- Alternativen? (z.B. Dienstleister)
Bei der Vielzahl an Herstellern und Druckverfahren fiel es nicht leicht, das für uns Richtige zu wählen. Es wurde auch recht schnell klar, dass es die „Eierlegende Wollmilchsau“ auch hier nicht gibt. Jedes Verfahren und Abwandlung der verschiedenen Hersteller davon haben ihre Vor- und Nachteile.
Generell kann man sagen, dass das Druckverfahren abhängig vom verwendeten Material ist und dieses wiederum von den geforderten Eigenschaften. Gerade die für und bei nass magnet wichtigsten Punkte, wie Druckdichtigkeit, Temperaturbeständigkeit bei zugleich kleinen Produkten mit engen Toleranzen, war so nicht in einem Gerät abzubilden.
Da Professionelle Polymer-3D-Drucker je nach Technologie zwischen 2.500€-65.000€ und Metall-3D-Drucker preislich noch deutlich darüber liegen, sollten solche Investitionen vorher genau überlegt sein und sich später auch amortisieren.
Nach einiger Überlegung und weiterer Recherche entschieden wir uns dann jedoch für ein relativ hochpreisiges Gerät, bei dem wir die wenigsten Abstriche machen müssen.
Doch dann kam Corona…
Auf Grund der sich zuspitzenden Corona-Lage im Frühjahr 2020 und der daraus resultierenden wirtschaftlichen Unsicherheit wurden erst einmal alle nicht produktionsrelevanten Investitionen auf unbestimmte Zeit verschoben. Da wir in der neuen Technologie aber auch bzw. gerade in wirtschaftlich schlechteren Zeiten einen gewinnbringenden Vorteil sahen und das Projekt nicht ganz zum Erliegen kommen sollte, suchten wir weiter nach einer Alternative…
Pilotprojekt 3D-Drucker-Bausatz
Das Pilotprojekt wurde ins Leben gerufen und wir entschieden uns für ein sehr günstiges Modell aus dem Hobbybereich, für knapp 200€ als Bausatz. Dieser beruht auf dem FDM-Verfahren (siehe FDM-Fused Deposition Modeling (Filamente)) und ist somit vom Handling sehr einfach und bürotauglich. Hiermit wollten wir die neue Technologie besser kennen-lernen und Erkenntnisse gewinnen, wo die additive Fertigung in der Unternehmung tatsächlich Anwendung findet.
Der Zusammenbau war sehr einfach, nach kürzester Zeit erledigt und der erste Einrichtungsdruck gestartet. Auch die ersten kleineren Testdrucke aus dem Internet liefen ohne Probleme und wir waren mehr als überrascht von der Oberflächenqualität und Genauigkeit der Teile. So machten wir uns in unseren Anlagenkonstruktionen auf die Suche nach einfachen Bauteilen die bisher auch aus Kunststoff, jedoch mit konventionellen Verfahren, hergestellt wurden. Bestes Beispiel ist hier eine RFID-Tag-Halter der auf unseren Umlaufanlagen auf jeden Werkstückträger (WT) sitzt. Der Tag dient der Codierung von Werkstückträgern und übermittelt bauteilzugehörige Daten zwischen WT und Anlage. Da jedes WT für jedes Produkt und Anlage individuell ist, gibt es hierfür keine Halter zu kaufen. Der Halter selbst ist keinerlei mechanischen Belastungen ausgesetzt, sondern dient ausschließlich zur Aufnahme des Tags, ist aber trotzdem notwendig.
Für die Twin Boost Anlagen, die vom Kunden in den letzten Jahren immer häufiger auf Grund steigender Nachfrage bestellt werden, werden pro Anlage im Hauptteil 30 Stück und in der Erweiterung weitere 15 Stück benötigt. Stellt man allein diese Teile im 3D-Druck her, wird relativ schnell deutlich, welches Einsparpotential mit der neuen Technologie möglich ist. Siehe Grafik:
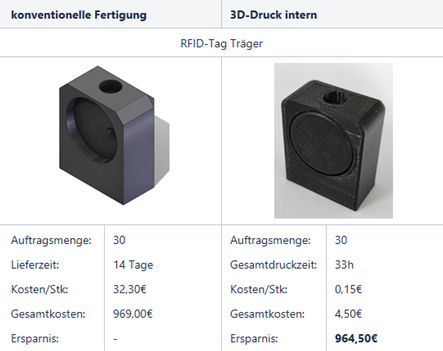
Die Schwächen…
Nach einigen hundert Stunden Druckzeit, zeigten sich jedoch langsam die Schwächen von so einem günstigen Gerät. Der Verschleiß der Führungen und weiteren Bauteilen, führten zu immer mehr Einrichtungs- und Betreuungsaufwand und immer mehr Drucke schlugen fehl, führte man diese arbeiten nicht sehr genau aus.
Neue Erkenntnisse aus dem Pilotprojekt
Durch die guten allgemeinen Erkenntnisse und Druckergebnisse aus dem Pilotprojekt ergab sich für uns ein ganz neuer Ansatz. Wir stellten fest, dass Teile aus dem günstigsten Verfahren, dem FDM-Verfahren, zwar optisch nicht am ansprechendsten, jedoch gerade für Prototypenwerkzeuge, Serienwerkzeuge, Verpackungsmuster und einzelne Komponenten im Vorrichtungsbau (Halterungen, WT-Führungen, Testaufbauten) vollkommend ausreichend sind.
Also entschieden wir uns für einen professionellen 3D-Drucker, den Raise3D E2, mit vielen automatisierten Funktionen und Industrie 4.0 Anwendungen. Dieser nutzt auch das FDM Verfahren und besitzt einen Dual-Extruder, der einen Doppel-, Spiegel- und Multimaterialdruck ermöglicht. Dieser ist auch bereits am Standort Hannover in Betrieb und aktuell voll ausgelastet.
Ausblick
Da nach und nach Anfragen aus anderen Bereichen kommen, ist für die Zukunft geplant, den 3D-Drucker als Ressource für andere Projekte zur Verfügung zu stellen. Dafür müssen weitere Mitarbeiter qualifiziert und eine Art „Druck Service“ erstellt werden. Um künftig noch festere Objekte zu drucken, gibt es beim FDM-Verfahren die Möglichkeit, faserverstärkte Filamente zu verwenden. Hierfür gibt es einfach Umrüstsätze für den Raise3D E2. Um Kunden Prototypen ihrer Produkte zur Verfügung zu stellen, wäre die nächste Überlegung beispielweise die Anschaffung eines SLA-Druckers, da sich hiermit sehr präzise, filigrane Strukturen und glatte Oberflächen herstellen lassen.
Neue Freiheiten als Konstrukteur
Bei der Designfreiheit von Bauteilen war man als Konstrukteur bisher durch fertigungsbedingte Restriktionen meist sehr eingeschränkt oder Aufwand/Kosten überstiegen den Nutzen. Bei der additiven Fertigung hingegen reduzieren Fasen, Radien und Freimachungen sogar den Materialverbrauch und die Druckzeit. Hinterschnitte und aufwändige Konturen sind jetzt kein Problem mehr und sogar interne Freimachungen, Umdrucken von z.B. Normteilen und Multimaterialien sind möglich.
Fazit
Da die additive Fertigung mittlerweile in knapp 50% der Unternehmungen weltweit genutzt wird, war es genau der richtige Schritt, Erfahrungen im Bereich der additiven Fertigung zu sammeln und die Vorteile dieser neuen Technologie kennen zu lernen. Auch wenn wir erst seit kurzem diese neue Fertigungstechnologie nutzen, ist diese bereits jetzt bei uns schon nicht mehr wegzudenken. Zum einen regt sie die Kreativität der Mitarbeiter an und ergänzt aktuell sinnvoll die konventionelle Fertigung von Teilen im Anlagenbau. Die Technologie schreitet zwar weiterhin rasant voran, eine Serienfertigung mit hohen Stückzahlen oder eine vollständige Ablösung traditioneller Fertigungstechniken ist jedoch noch nicht in Sicht.
Robin Paetz,
Prozessentwicklung, nass magnet GmbH