Qualität? Gesichert!
HU senkt die Ausschusskosten
Nach dem Wechsel der Geschäftsführung im Jahr 2017 und der Einstellung einer Reihe neuer Fachkräfte war die Abteilung Qualitätssicherung der nass magnet Hungária Kft. endlich in der Lage, die Qualitätsziele des Unternehmens ohne externen Input zu erfüllen.
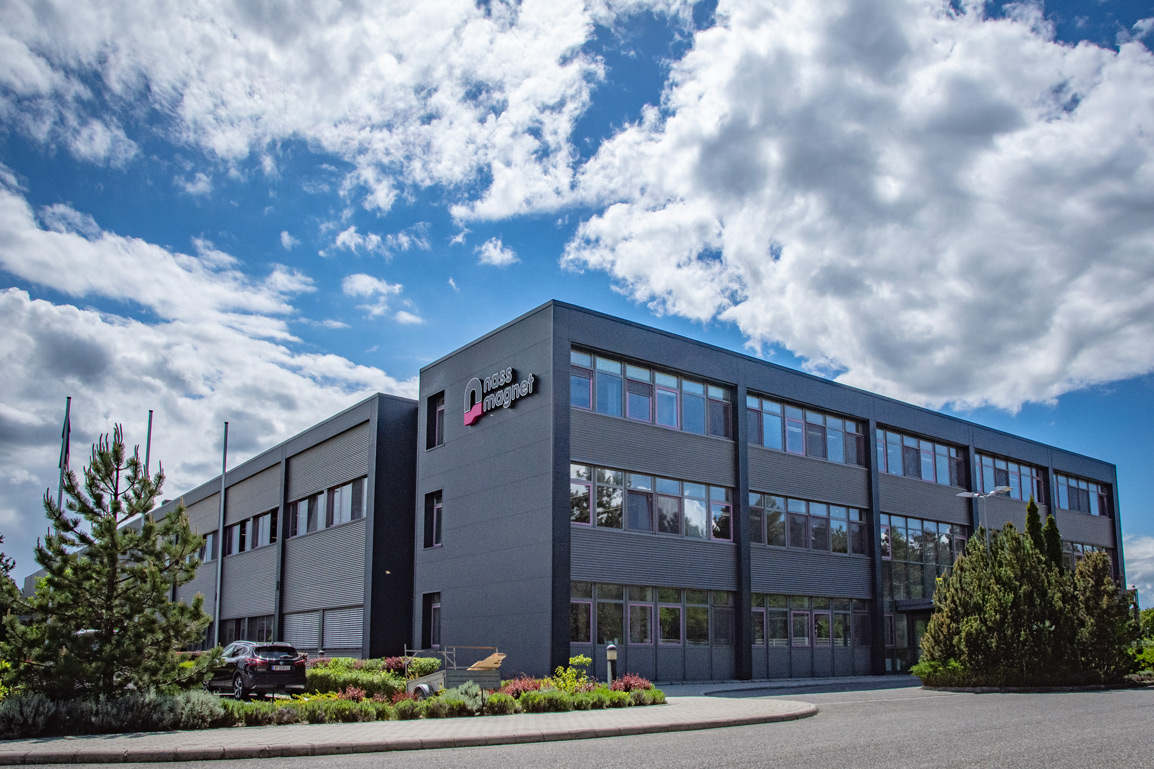
Nun stehen der Qualitätssicherung in Ungarn alle notwendigen Ressourcen zur Verfügung, um mit der anstehenden Aufgabe tatsächlich voran zu kommen. Der Personalmangel in den vergangenen Jahren hatte leider zur Folge, dass die QS-Abteilung des ungarischen Werks beinahe auf der Stelle trat. Sie konzentrierte sich Tag für Tag vor allem darauf, auftretende Probleme zu erkennen und zu beheben. Für die Umsetzung von Präventivmaßnahmen blieb einfach keine Zeit.
Langfristige Kostensenkungen können nur durch kurzfristige Kostensteigerungen erzielt werden. So wurde in der ungarischen Abteilung Qualitätssicherung im April 2018 jeweils ein neuer Qualitätstechniker sowie ein Endprüfer pro Schicht eingestellt. Dank ihrer Verstärkung durch neue Mitarbeiter ist die QS jetzt in der Lage, alle Produktionsbereiche abzudecken, wie die Grafik verdeutlicht.
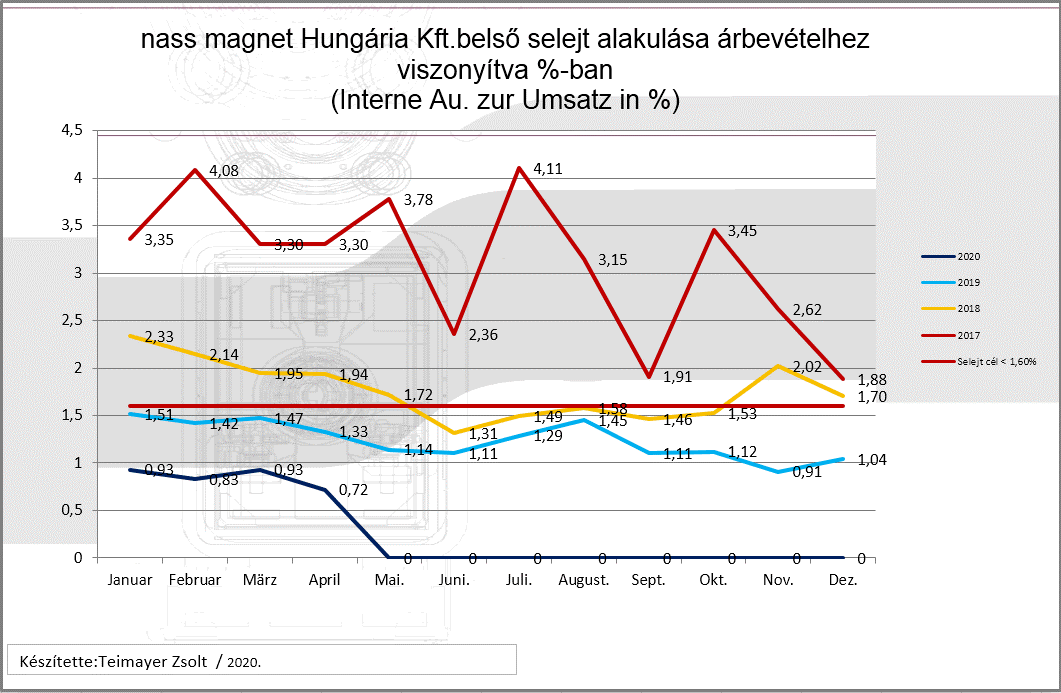
Unsere täglichen Aktivitäten
Eine der Grundvoraussetzungen für einen reibungslosen Produktionsablauf ist die zeichnungsgerechte Verfügbarkeit der Komponenten. In den meisten Fällen werden die Rohstoffe einer Wareneingangskontrolle unterzogen, bevor sie eingelagert und in der Produktion eingesetzt werden.
Dieser Vorgang umfasst die regelmäßigen Wareneingangskontrollen selbst (mehr als 300 Produkte pro Monat) und beinhaltet zusätzlich die Dokumentation der Mengensteigerungen sowie die Bemusterung von eigen- und fremdgefertigten Komponenten. Für die Prüfung von Formteilen sowie die Überwachung als auch Wartung von Messgeräten werden zwei Mitarbeiter benötigt.
Unser Messlabor und dessen Ausstattung ist auf die Anforderungen unserer Produkte zugeschnitten. Seine Einrichtungen erlauben es derzeit, alle Größen und Qualitäten (mit Ausnahme der Rohstoffprüfung) zuverlässig zu messen. Bei der Beschaffung unserer Messgeräte haben wir uns, um eine durchgängige Interoperabilität der Messsysteme zu erreichen, so weit wie möglich für Geräte entschieden, die bereits am Standort Hannover im Einsatz waren.
Die interne Ausschussrate im Verhältnis zum Umsatz lag im Jahr 2017 bei durchschnittlich 2,61 Prozent, was einem Betrag von 565.000 Euro entspricht. Das in der BSC* für 2018 festgelegte Qualitätsziel von 2 Prozent war also eine große Herausforderung für uns, der wir uns jedoch in bewundernswerter Weise gestellt haben.
Aktivitäten und Maßnahmen zur Reduzierung der Ausschussmenge
Die Aufgabe und Ziele waren klar und so machten wir uns daran, eine Lösung zu finden. Der erste Schritt in diesem Prozess war die Festlegung eines produktspezifischen Ausschuss-Codes für jede Arbeitsstation in der Produktion. Die Theorie schien zunächst nicht allzu kompliziert zu sein, doch in der Praxis musste ein brauchbarer Ausschuss-Code generiert werden, der für alle MitarbeiterInnen gleichermaßen gilt. Dieser Code ermöglicht es, Mängel oder Ausfälle sowie alle erwarteten Ergebnisse genau zu identifizieren. Um ihn verwaltbarer zu machen, darf der Ausschuss-Code darf nicht zu viele „Attribute“ enthalten. Diese Aufgabe erwies sich bei weitem nicht als einfach, insbesondere wenn man bedenkt, dass jeder einzelne Arbeitsplatz berücksichtigt und mit einbezogen werden musste.
Nachdem ein Konsens erzielt und die Codes von allen Parteien akzeptiert wurden, musste das Personal in der dessen Auslegung geschult werden. Die neu festgelegten Codes für jeden der Arbeitsplätze mussten dann in das SAP-System eingegeben werden, um die Menge des während jeder Schicht anfallenden Ausschusses zu erfassen.
Es galt sicherstellen, dass die neue Arbeitsweise mit den Ausschuss-Codes für die gesamte Belegschaft verständlich und nachvollziehbar ist sowie dass sie von allen fachgerecht umgesetzt wird. Das neue Codierungssystem ermöglicht eine korrekte Identifizierung der Teile – in den zwei Monaten davor musste jedes einzelne Ausschussteil von der QS geprüft, in Gruppen eingeteilt, neu vermessen und charakterisiert werden.
Wie wir es geschafft haben
Wir erkannten, dass der effizienteste Ansatz zur Erzielung einer Einsparung darin bestand, unsere Umstrukturierungsbemühungen bei dem Spritzgussverfahren zu beginnen, da dieses den letzten Schritt in unserem Produktionsprozess darstellt und in dieser Phase die zeitaufwändigsten Vorgänge stattfinden. An dieser Stelle wird die größte Anzahl von Teilen eingebaut.
Für die Fehler wurde eine ABC-Analyse** durchgeführt und ergab, dass die meisten Defekte und Ausfälle beim Start oder Neustart der Maschine auftreten. Beim Spritzgießen entsteht Anlaufausschuss während der ersten „Einspritzungen“ - normalerweise führen die ersten zwei oder drei Produktionsversuche zu Ausschuss, weil die Formhohlräume noch nicht vollständig gefüllt sind, die Zykluszeit noch nicht ganz stimmt und der Prozess noch nicht stabil ist.
Um die Ausschussmenge bei Maschineneinstellungen weiter zu reduzieren, mussten zusätzliche Maßnahmen ergriffen werden. Daher haben wir beschlossen, dass der Ausschuss unserer Automobilprodukte, bei welchem Schweißabfälle (das Schweißen des Produktes sollte validiert werden) entstehen, für eine weitere Verwendung aufbereitet und nicht entsorgt werden sollte. Das Produkt kann dann als Adapter für den Spritzgussprozess verwendet werden. In gewissem Sinne kann dies als Recycling verstanden werden, da der Ausschuss wiederverwendet wird.
Der Aufbereitungsprozess und die weitere Handhabung dieser Ausschussteile erfordern eine besondere Sorgfalt. Deshalb mussten wir einen separaten Prozess entwickeln, welcher eine mehrstufige Reihe von Kontrollen umfasst. Außerdem mussten wir dem Personal beibringen, wie das neue System funktioniert. Als Ergebnis dieser Maßnahmen können wir heute, je nach Anzahl der hergestellten Produkte, allein im Automobilsektor bereits mehrere hundert Euro einsparen.
**ABC-Analyse = auch Programmstrukturanalyse genannt, ist ein betriebswirtschaftliches Analyseverfahren
zum Teilen einer Menge von Objekten in die Klassen A, B und C.
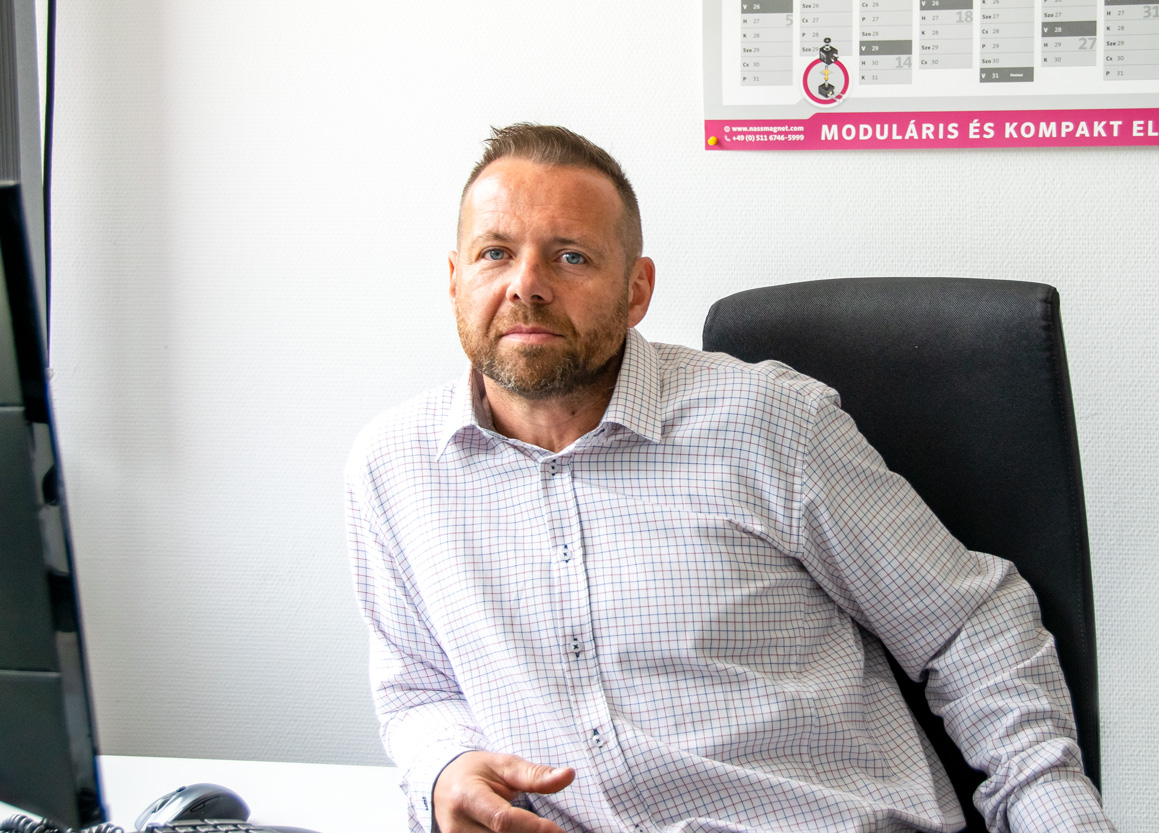
Die neue Prämie für Qualität
Wir sind uns im Klaren, dass MitarbeiterInnen der Schlüssel zum Erfolg unserer Fertigungsprozesse sind. Wenn wir die Ausschussmenge weiter reduzieren wollen, sollten alle Mitarbeitende aktiv in den Prozess der Aufrechterhaltung hoher Qualitätsstandards einbezogen werden und Anreize erhalten, dies zu tun. Aus diesem Grund haben wir einige Änderungen an der vierteljährlichen Prämie vorgenommen:
Um das Qualitätsbewusstsein der Belegschaft weiter zu fördern, wird die gesamte Prämie nun auf der Grundlage einer 50/50-Aufteilung zwischen Produktions- und Qualitätskennzahlen berechnet.
Als Teil des Anreizsystems basiert die Qualitätsprämie auf den Ausschusskosten im Verhältnis zum Umsatz. Je niedriger die Rate, desto höher die Prämie. Die exakte Prämie ergibt sich aus den vier verschiedenen Qualitäts-Faktoren Verschrottungen, Kundenreklamationen, Nacharbeitsstunden und Ausschusskosten.
Die Monitoring-Checkliste
Eines der grundlegenden Prinzipien der Physik ist die Idee, dass Bewegungen immer den Weg des geringsten Widerstandes geschehen. Dasselbe kann man auch von Menschen behaupten. Wir stellen sicher, dass unsere MitarbeiterInnen während des Produktionsprozesses stets die vorgeschriebenen Komponenten verwenden, alle notwendigen Kontrollen durchführen und die Arbeitsanforderungen jederzeit einhalten.
Wie Stalin einmal sagte, basiert Vertrauen auf regelmäßigen Überprüfungen, deshalb haben wir eine „Überwachungs-Checkliste“ für unsere Qualitätsprüfer eingeführt, die sie bei ihren täglichen Arbeitsplatz-audits verwenden können. Unsere bisherigen Ergebnisse bestätigen, dass alle ihre Arbeit ordnungsgemäß ausgeführt haben; der wichtigste Leistungsindikator bestätigt dies sogar mit einer Erfolgsquote von 99% im dritten Quartal 2019.
Erste Erfolge
Nehmen wir unser Produkt System 8 Magnetspule als Beispiel: Hier lag der Ausschussanteil auf Grund eines Drahtbruchs bei 4-7%. Durch die Neudefinition der Drahtwickelhöhe konnten wir die Ausfallrate und den damit ver-bundenen Ausschuss auf 1,3% reduzieren.
Natürlich gibt es immer noch Produkte, die Potenzial zur Verringerung ihres Ausschusses haben. Eines meiner Lieblingsprodukte ist das C-13, dessen Ausschussrate seit seiner Einführung noch nie unter 10 Prozent gesenkt werden konnte. Dank des neuen modifizierten Rohstoffes ist aber ein Licht am Ende der Tunnels zu erkennen. Nach der Einführung des neuen Ausgangsmaterials ist eine Ausschussrate von nur noch 5 bis 7 Prozent zu erwarten.
Wir arbeiten derzeit daran, Probleme, Widerstandsdefekte und Fehler für alle unsere Produkte innerhalb weniger Jahre zu reduzieren sowie teilweise sogar vollständig zu beseitigen. Wenn wir dies erreichen, werden wir in der Lage sein, jedes Jahr Tausende weiterer Produkte vor dem Ausschusshaufen zu bewahren.
Eine gute Zwischenbilanz
Als Ergebnis dieser Maßnahmen konnten wir in knapp zwei Jahren die jährlichen Ausschusskosten von insgesamt 565.000 Euro (2,61%) auf rund 320.000 Euro (1,3%) senken. Die folgende Auswertung zeigt, wie sich unsere Kosten in den folgenden zwei Jahren verändert haben. Für 2019 wurde ein Wert verwendet, der auf dem Durchschnitt der letzten 9 Monate basiert.
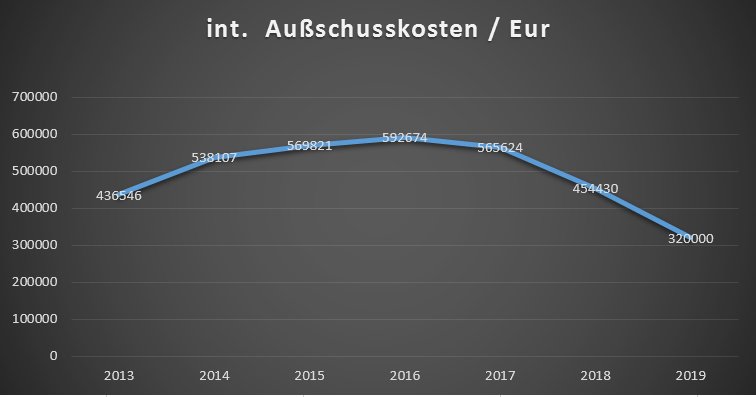
Stabile Qualität, weniger Reklamation, bessere Ergebnisse
Zusammenfassend kann man sagen, dass eine stabile, hochwertige Produktion mit einer geringen Anzahl von Kundenreklamationen und minimalem Ausschuss sowie möglichst geringer Nacharbeit nur dann zu erreichen ist, wenn
- robuste Produkte konstruiert und die Maßtoleranz unter Berücksichtigung der Fertigungswerkzeuge und -technologie bestimmt werden. Je weniger „Spielraum“ in der Fertigung besteht, desto höher der Aufwand, um gute Produkte fertigen zu können.
- das Wissen und Qualitätsbewusstsein der Belegschaft kontinuierlich gestärkt und aufrechterhalten wird. Zu diesem Zweck finden regelmäßige Schulungen statt.
- wir Zeit, Geld und Energie in die ordnungsmäßen Zustände aller Anlagen investieren und präventive Wartungsarbeiten durchführen, um unerwünschten Fehlfunktionen bereits im Vorfeld zu vermeiden.
- Qualität im Voraus in das Produkt hinein konzipiert wird, da diese nicht im Nachhinein integriert werden kann. Ohne diese Qualität können Produkte nur mit einem hohen internen Ausschuss, Nacharbeit und Kundenreklamationen hergestellt werden.
Wir sind uns bewusst, dass unser Spielraum zum Reduzieren von Ausschuss nicht endlos ist und dass wir früher oder später an die Grenze unserer Möglichkeiten stoßen werden. Es gilt, das Optimum zwischen Kosten für den Ausschuss sowie dessen Beseitigung zu finden. Bis dahin gibt es noch diverse Makel zu korrigieren und die Potenziale einiger Produkte weiter auszuschöpfen.
Im Laufe der Jahre wird der Umfang der Reduzierung des Ausschusses immer geringer. Mit der Zeit wollen wir jedoch die Philosophie von KAIZEN** anwenden, indem wir uns das Prinzip der kontinuierlichen Verbesserung zu eigen machen. Wir müssen uns so schulen, dass wir auch die kleinsten Verbesserungsmöglichkeiten erkennen.
**KAIZEN = japanische Lebens- und Arbeitsphilosophie sowie ein methodisches Konzept um das Streben nach kontinuierlicher und unendlicher Verbesserung
Wir wollen immer bessere Ergebnisse liefern, um die Erfolgsgeschichte unserer Produkte weiterzuführen. So verstehen wir Fortschritt bei nass magnet.
Zsolt Teimayer
Leitung Qualitätssicherung,
nass magnet Hungária Kft.